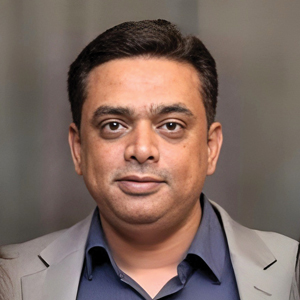
Mother India Forming Innovates Customized Steel Solutions
Mother India Forming has transformed from a standard ERW steel tube manufacturer to a global leader in custom solutions, driven by innovation, advanced technology, and customer-centric philosophy. – Santosh V, Director of Sales, Mother India Forming Pvt. Ltd.
Can you tell us about the evolution of Mother India Forming from a standard ERW steel tube and simple roll-formed profile manufacturing facility to a producer of customized steel tubes?
Mother India Forming has undergone a remarkable evolution and is fueled by innovation and a customer-centric approach. The company has transformed into a leader in customized steel tubes and profiles and components. From its roots in conventional manufacturing, Mother India Forming has embraced advanced technologies and harnessed skilled expertise to redefine industry standards. The company now crafts customized tubes, profiles and complex components and caters to a spectrum of industries, from automotive to construction and beyond. This journey, from standard to bespoke, represents a rewriting of possibilities in the dynamic realm of cold roll-formed components, showcasing the adaptability and innovation that define Mother India Forming’s trajectory.
What sets your company apart in the industry, in view of four decades experience in shaping sheet metal?
Mother India is a leading organization with over 4 decades with innovation as its hallmark and has been making customized tubes and ready to use components for the past 2 decades now. Today we have evolved as a One-Stop Solution for all roll forming needs, and our operations are fully integrated. Right from concept to developing a component with computer-aided design, ideas are digitally conceptualized using the most advanced simulation software. By localization of safety critical parts in Construction Equipment, Form Works, elevators, Road Safety components and others, we have become front runners in the roll-forming industry.
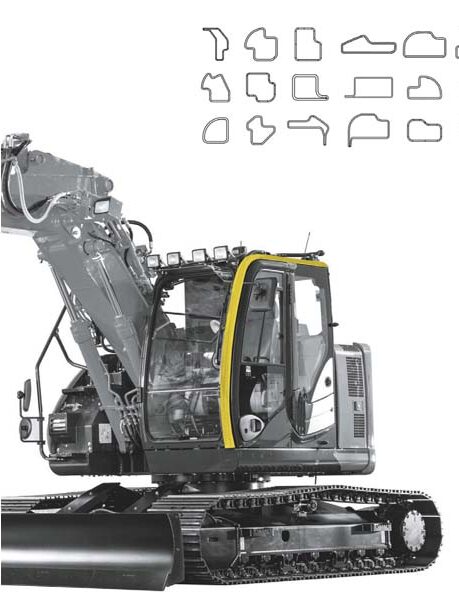
Could you elaborate on the industries you serve, such as automotive, construction equipment, elevator, and others, as well as the products you create for them?
At Mother India Forming, our commitment to precision cold roll forming resonates across diverse industries, where cutting-edge machinery and a skilled team converge to craft tailored solutions with quality and cost effective components. Below are some key sectors we serve.
Construction Equipment: Employing cold roll forming techniques, we manufacture A pillars, B pillars, structural elements, Roll Over Protected structures (ROPS) and Fall Over Protected Structures (FOPS) vital to operator cabins for construction machinery.
Road safety components: Our Delineators are a common sight in major highways across India.
Form Works for Infrastructure: Our localized Formworks profiles play a pivotal role in shaping infrastructure, offering a cost-effective and versatile solution for various construction projects.
Elevator Industry: Playing a key role in vertical transportation industry, we manufacture components such as hollow guide rails, door stiffeners, and track profiles using advanced roll forming.
Automotive: Our high strength, light weight tubes are used by leading bus body manufacturers in India. These precision roll formed tubes and profiles meet stringent safety and quality standards.
Custom Solutions: Beyond the highlighted sectors, Mother India Forming provides custom roll forming solutions. Whether for, Textile machinery, Storage solutions, Electric cabinets, Home appliances, or other specialized applications, we bring precision and reliability to every project.
How have advancements in technology and equipment, such as laser cutting and powder coating, contributed to your manufacturing capabilities and product quality?
The addition of tubular Laser cutting and conveyorized powder coating used in post processing of cold rolled products adds value and provides a one stop solution for OEMs. This also provides better control on quality and cost of the components.
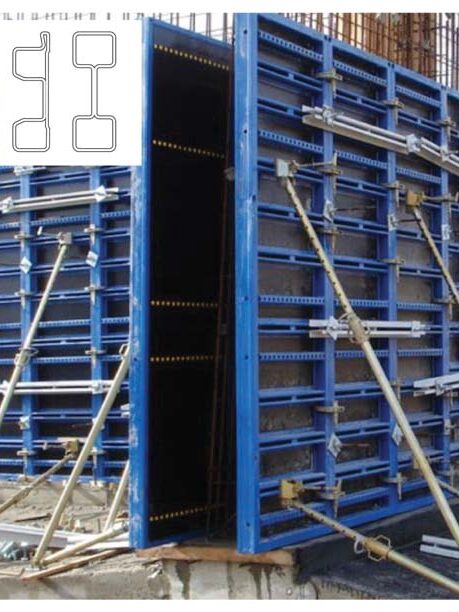
Could you explain what does ‘localization of roll formed components’ means, and how it benefits your clients?
The “localization of roll-formed components” by Mother India Forming, in harmony with the Make in India initiative, involves producing these components within the country. This strategy benefits clients by reducing costs, shortening lead times, and supporting the broader national movement. Clients enjoy cost efficiency, faster project timelines, and the ability to contribute to the local economy. The approach fosters customization, collaboration, and supply chain resilience, ensuring high-quality standards. Moreover, local production enhances job creation, supports economic growth, and minimizes the environmental impact associated with transportation. By choosing locally sourced roll-formed components, clients align with a sustainable, efficient, and nationally beneficial manufacturing process and further enhances OEMs to export finished products to the rest of the world.
As a source of global supplies to leading OEMs, what measures have you taken to ensure quality and consistency in your products for a global market?
The Construction equipment and vertical transport segment is a regulated and competitive industry that requires suppliers to meet various standards and norms. Some of them are:
Quality management system: We have certified quality management systems that complies with ISO or equivalent standards
Safety and performance: Our components meet the safety and performance requirements of relevant codes and standards.
Environmental and social responsibility: We follow the principles of environmental and social responsibility like reducing waste and emissions, using renewable energy sources, respecting human rights and labour laws, etc.
Innovation and technology: Our ability to innovate and adopt new technologies enhances the efficiency, reliability, and sustainability of products.
Mother India Forming has adopted and strictly adheres to these norms.
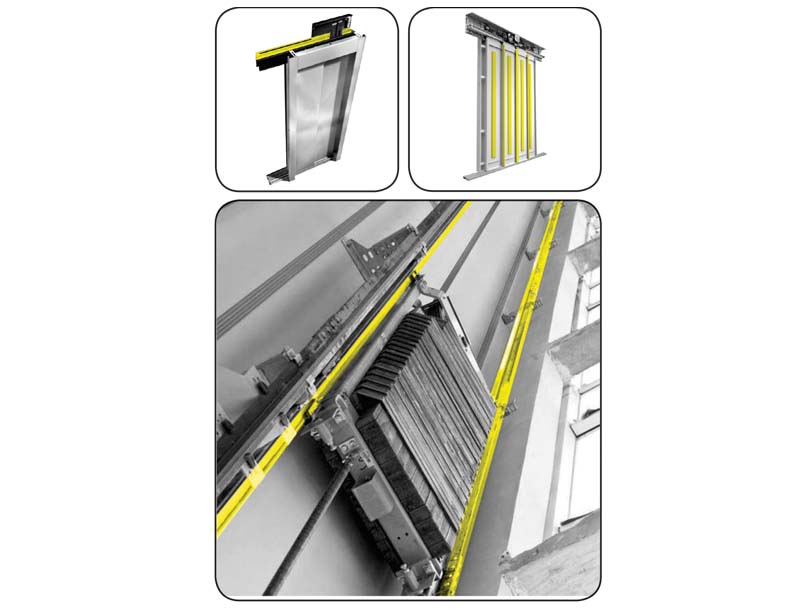
Can you discuss the current market trends and challenges in the sheet metal and customized steel tube manufacturing industry, and how Mother India Forming is addressing them?
A primary challenge most sheet metal industries face is the price of steel being higher and product demand being low in India than at China, resulting in low growth rate of industries in India.
Mother India Forming navigates industry trends by embracing Industry 4.0. The company has invested in IoT-enabled systems to enhance efficiency and optimize operations.
Sustainability is a cornerstone, with practices like roof top solar panels to generate power, recycling scrap metal and energy-efficient processes aligning with global eco-friendly manufacturing demands.
What are your future plans for expansion and growth, both in terms of market reach and product offerings?
Mother India Forming’s future expansion involves a dual focus on market reach and product offerings. Internationally, the company plans strategic market penetration and entry, exploring opportunities to be a global business partner. An online presence and regional offices aim to enhance accessibility and foster relationships. Innovative customization solutions, diversified product lines, and strong R&D investments underscore a commitment to staying ahead in the market. Strategic partnerships, Value Analysis and Value Engineering programs, and a focus on customer success contribute to a holistic growth strategy, positioning Mother India Forming as an industry leader in precision cold roll-formed components.